Careers at Promex
Careers at Promex
Promex Industries and its QP Technologies Division offer competitive salaries, flexible working hours, and good benefits – including 401K and medical/dental insurance.
Promex Industries is an Equal Opportunity/Affirmative Action employer.
Create the Impossible With Us!
We are looking for talented individuals to join our team at Promex Industries, where we turn ideas into life-changing devices and make the impossible possible. Are you excited to be part of a dynamic team that transforms concepts into reality? At Promex, you’ll have the opportunity to work on cutting-edge microelectronics assembly projects that help enhance lives.
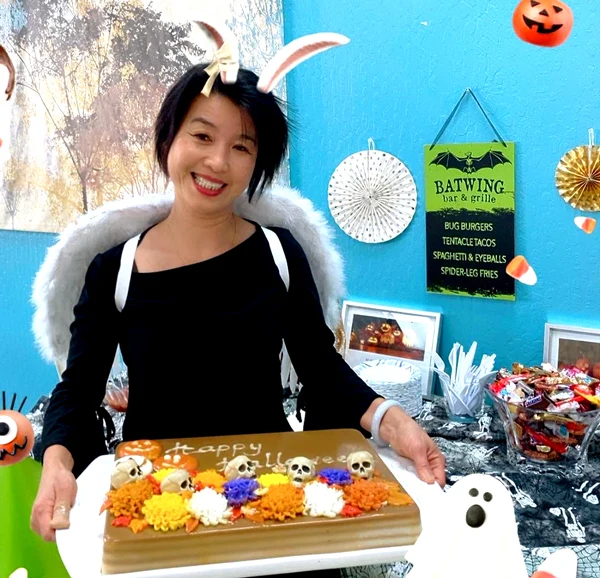
Reasons To Work At Promex
- Competitive Salaries
- Flexible Working Hours
- 401k Benefits
- Medical / Dental Insurance
- Work-Life Balance
Reasons To Work At Promex
- Competitive Salaries
- Flexible Working Hours
- 401k Benefits
- Medical / Dental Insurance
- Work-Life Balance
Career Opportunities
We are currently seeking dedicated professionals to join us. If you’re up for the challenge, send your resume and cover letter to careers@promex-ind.com, with the position name in the subject line. Don’t miss out on the chance to shape the future with us!